The equipment is applicable to the recycling of waste tires and waste rubber products. The anaerobic pyrolysis technology is used to decompose the high molecular polymer in the waste tire. The high molecular polymer breaks after the thermochemical reaction and returns to the state of small molecule or monomer to produce the pyrolytic gas, pyrolytic carbon and steel wire. The non-condensable gas enters the combustion chamber for combustion and heating. The burning high-temperature flue gas absorbs most of the heat energy through the main pyrolysis furnace and enters the back-end flue gas system for treatment and then is discharged after reaching the standard. The condensable gas forms pyrolytic tar. On the premise of safety, environmental protection, continuous and stable operation, the harmless and reduced recycling of waste tires and waste rubber products is realized.
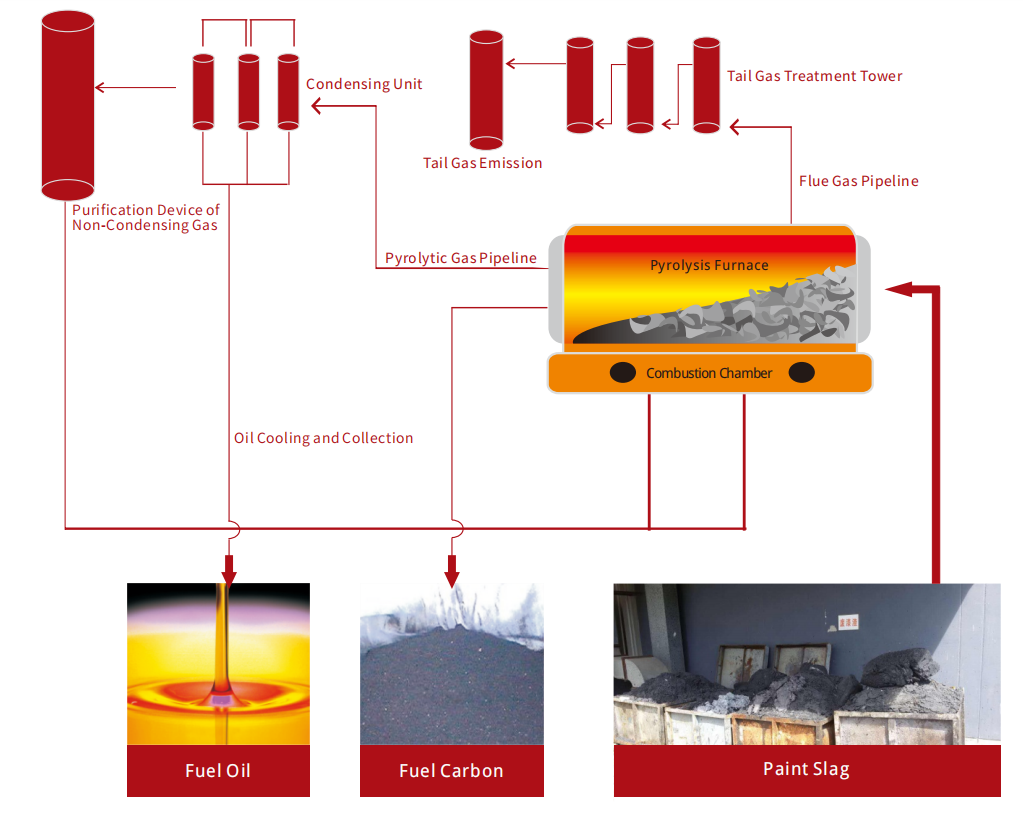
Complete equipment is mainly comprised of:
Pretreatment system, pyrolysis module, oil receiving module, non-condensable gas purification heat utilization module, flue gas treatment module and electrical control module.
The waste tire recycling production line is composed of various types of heavy equipment. Its function is to automatically separate rubber, steel wire and fiber materials from car tires, truck tires and engineering tires.
The system adopts the crushing and sorting method to recover waste tires and carry out resource recovery and secondary application. It can realize tire crushing, steel wire separation and fiber separation, so as to obtain fine rubber particles, which can effectively deal with waste tires, and the coexistence of resource recycling and environmental protection.
Technical Features
The whole line is of modular design, and the automation of production and maximization of output are realized through the automatic control system.
Ring Cutting + Thread Rolling Module
The bead cutter cuts out the inner bead of the tire so as to prolong the service life of the subsequent crushing equipment and improve the production efficiency; the thread rolling machine separates the steel wire in the bead to improve the value of the product.
Waste tire Crushing Module
The waste tires with the stop ring removed are transported to the double shaft shredder through the conveyor. The two groups of cutters rotated by the double shaft shredder cut them into rubber strips, and the rubber strips are transported by the conveyor to the disc screen for sorting. The rubber blocks larger than the gap are returned to the double shaft shredder through the conveyor for crushing again, while the rubber blocks smaller than the gap are transported to the buffer bin through the conveyor. The buffer bin can adjust the buffering capacity to ensure that the next module can be fed evenly.
Steel Wire Separation Module
The rubber blocks in the buffer bin are evenly transported to the steel wire separator through the conveyor and finely crushed into a mixture of rubber particles ≤ 16mm and steel wire. In the process of finely crushing, the steel wires are separated from the rubber according to the working principle of shearing and extrusion. The separated rubber particles ≤ 16mm are transported to the subsequent process through the conveyor, and the steel wire is output through the conveyor.
Note: the particle size can be adjusted as required by customers.
Dust Removal Module
In the crushing process of waste tires, we will use negative pressure to collect the dust at the main places where the dust is generated, so as to ensure that the dust generated in the production process can be effectively treated.
Automatic Control Module
The automatic control system is used to intelligently control and integrate each single machine of the crushing production line, so as to match the production capacity of each production stage, and maximize the installed power, so as to realize the automation of the production process and maximize the output.
Rotary kiln, Hot blast stove heating, Indirect heating, Step heating; Medium and low temperature, Atmospheric pressure, Oxygen-free environment; Continuous type and batch type
Item |
Details |
Input Raw Material |
Automobile tires, engineering tires and other waste rubber products |
Final Product |
Pyrolytic tar: 1. Used as raw material oil for refinery; 2, directly as fuel oil. Pyrolytic carbon: carbon processing raw material Steel wire: Furnace steelmaking; Sandblasted steel shot Non-condensing combustible gas: reused in the system |
Capacity |
As reuired |
Operating Model |
Continuous Model (feed, discharge, operation); Batch Model |
Heating Mathod |
Indirect heating, adjustable constant temperature heating |
Energy |
Non-condensing gas, natural gas |
Main furnace material |
Stainless steel inner cylinder |
Operating Pressure |
±500Pa |
Pyrolysis Temperature |
400~600℃ |
Automation |
PLC/DCS Control, fully automatic intelligent control, low labor intensity |
Environmental Protection |
All emissions are in line with the most stringent local emission index requirements |